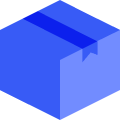
Logistics Service Providers (LSPs) and Packaging and Container businesses that specialize in servicing the Pharma industry and Cold Chain vertical.
Learn more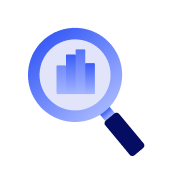
Contract Manufacturers that provide the infrastructure for drug design and development as a service, through various stages of clinical trials and approvals.
Learn more
Pharmaceutical businesses responsible for design, development and manufacturing of prescription and over the counter products as well as specialty medicine like vaccines, biologics, cell & gene and radio therapies.
Learn more